Products
Manufacturer and Fabricators of Oilfield Engineering Products
PetroSan Clamp + Sleeve + Coupling manufacturer in Norway
PetroSan Oilfield Engineering Co. was founded in 2020 and is a well known precise manufacturer and fabricators of pipe insert sleeves, tube insert sleeves (Ferrule), pipe repair clamps, fabricated fittings, line stop hot tapping fittings, pipe spools, High-pressure repair split sleeve, Flange Leak Repair Clamp, Alloy 601 Tube Inserts or Ferrule, Alloy 602ca Tube inserts or ferrule, pipe spool , Miter Bend , pipe half reinforcement sleeve, mij, a694 heavy flanges, Duplex Flanges, taper tube plug , pipeline pigs , Tank and pressure vessel, piping skid fabrication and piping fabrication in a variety of ferrous and non-ferrous grades of carbon steel, stainless steel, and high nickel alloys. The company is certified by TUV Nord Norway under ISO 9001: 2015 and is widely recognized in the industry. We create our items using the newest technologies while keeping complete control over the quality of the goods in Norway.

A covering that shields a pipe from corrosion, abrasion, and other dangers is called a pipe insert sleeve. It is a cylindrical barrier that is placed inside the pipe to protect both the internal coating and the goods being conveyed.
An industry leader in the production and distribution of premium pipe sleeves, Petrosan is also a manufacturer of pipe insert sleeves, pipe internal insert sleeves, pipe internal protect sleeves, insert sleeves, corrosion-protective insert sleeves, and pipe weld joint insert sleeves.
A variety of professional pipeline insert sleeves are manufactured and supplied by PetroSan Oilfield Engineering Co. A PetroSan pipe insert sleeve, sometimes referred to as an internal pipe sleeve, is a pipe fitting made to guard against corrosion and damage to a pipe’s inside coating, particularly at welded joints.
Purpose:
Protection: The primary function of a pipe insert sleeve is to act as a protective barrier, shielding the internal coating of the pipe from damage caused by weld spatter, abrasion, and other potential hazards.
Corrosion Prevention: It helps prevent corrosion at the girth weld area, where the internal coating might be vulnerable.
Coating Integrity: By providing a barrier, the sleeve ensures the integrity of the internal coating, which is crucial for the long-term performance and lifespan of the pipeline.
Materials:
Common Materials: Pipe insert sleeves are typically made from robust materials like carbon steel, stainless steel, or other corrosion-resistant materials.
Customization: They can be customized to match the specific requirements of the application, including the pipe size, material, and coating type.
Applications:
Internally Coated Pipelines: They are commonly used in pipelines that have an internal coating to protect against corrosion, such as those used for transporting liquids, gases, or other materials.
Various Industries: These sleeves are used in a wide range of industries, including oil and gas, water, chemical, and industrial applications.
Benefits:
Extended Lifespan: By protecting the internal coating and preventing corrosion, pipe insert sleeves contribute to a longer lifespan for the pipeline.
Reduced Downtime: They help prevent costly repairs and downtime associated with corrosion or coating damage.
Cost-Effective Solution: While they are a specialized component, pipe insert sleeves can be a cost-effective solution for protecting the integrity of internally coated pipelines.
PetroSan Manufacture and supply pipe internal sleeve in Norway, pipe sleeve in Norway, FBE coated pipe sleeve in Norway, internal coated pipe fit sleeve in Norway, internal piping sleeve system in Norway, corrosion free insert sleeve in Norway, corrosion protection insert sleeve in Norway, long live piping insert sleeve in Norway.
Repairing a leak According to PetroSan, a leak repair split clamp, also called a split sleeve repair clamp, is a tool used to enclose and seal off isolated pipeline leaks, providing a long-term fix for corroded or damaged pipes.
Special requirements for leak repair split clamps include making sure the clamp is compatible with the pipe material and fluid, choosing the right sealing materials, and making sure the clamp can tolerate the operating temperature and pressure—double row sealing may be necessary for critical applications.
Leak repair split clamps come in various types, including split sleeve, bell joint, elbow, tee, and pinhole repair clamps, each designed for specific pipe configurations and leak types.
Split-sleeve or clamp leak repairs provide a number of benefits, such as being an affordable, efficient, and somewhat simple way to fix pipeline leaks—even when they are still in use—and being suitable for both short-term and long-term fixes.
PetroSan Oilfield Engg. Co. is manufacturer and suppliers high class pipe leak repair split clamp in Norway, bolted split sleeve in Norway, pipe capsulation split clamp in Norway, astm a516 gr.70 clamp in Norway, two half leak repair split clamp in Norway, high pressure split bolted clamp in Norway, Clamp for repair of leaking underwater pipelines in Norway, Leak Repair Clamp (LRC) in Norway, Pipe Repair Clamps in Norway, Pipeline Clamps Repair in Norway, High Pressure Repair Clamps in Norway, Split Sleeve Clamps in Norway, SPLIT+SLEEVE emergency bolt-on pipeline repair fitting in Norway, Mehanical Clamp repair design for a leaking pipe in Norway, Subsea Pipeline Repair Clamps in Norway, Pin Hole Leak Repair Clamps in Norway, Pipeline Leak Repair Clamp in Norway, High quality pipeline repair and maintenance split sleeve + clamp in Norway.
Without having to shut down the pipeline or replace the existing flanges, a flange leak repair clamp is a tool for sealing and fixing leaks in flange gaskets.
Here’s a more detailed explanation:
Purpose:
Flange repair clamps are designed to address leaks in flange gaskets, which are common in pipelines and other industrial systems.
Mechanism:
These clamps typically encircle the flange set and seal the leak by applying pressure and sometimes injecting a sealant through ports.
Benefits:
Reduced Downtime: They allow for leak repairs without shutting down the pipeline, minimizing operational disruptions and costs.
Permanent Repair: Some clamps are designed for permanent repairs, offering a long-term solution to flange leaks.
Versatility: They can be used on various flange types and sizes, both onshore and offshore.
Types:
Split-Sleeve Clamps: These clamps are split into two halves that can be clamped around the flange set.
Sealant Injection Systems: Some clamps incorporate sealant injection ports to seal the leak from the outside.
Applications:
Flange repair clamps are used in various industries, including oil and gas, water, and chemical processing, where pipelines and flange connections are common.
Specifics:
For subsea applications: Flange clamps are designed to repair leaking subsea flanged joints using a combination of a low profile, hinged clamp design and an innovative sealant injection system.
For onshore gasline leaks: Flange repair clamps can be used to seal leaks in flanges, including leak sealing compound injection ports, pressure gauge, and clamp installation supervision.
PetroSan Manufacture and supply high quality flange repair clamp in Norway, manufacturer of flange leak repair clamp in Norway, manufacturer of flange repair ring clamp in Norway, manufacturer of flange fit clamp in Norway, manufacturer of flange leak tight clamp in Norway, manufacturer of metal flange clamp in Norway, manufacturer of high pressure leak repair flange clamp in Norway, manufacturer flange seal split clamp in Norway, manufacturer flange split sleeve clamp in Norway, manufacturer flange joint repair clamp in Norway.
Pilot Pin-Hole Leak Repair Clamps, which come in standard sizes ranging from 2″ to 48″ and for pressures up to 153 Bar, are designed to repair process pipework in oil and gas process facilities for holes or faults up to 12 millimeters.
Simple encircling sleeves can be used to reinforce a defective pipe section. The sleeves fit closely to the pipe’s outside diameter and are shaped like two halves. The two halves are joined longitudinally by welding (backing strips are used for longitudinal welds to prevent mechanical property changes or weld-induced damage at the pipe surface). Additionally, the sleeve needs to be completely seal-welded to the pipe for applications involving pressure containment.
The “stand-off” repair clamp is the most widely used type of pipe repair component. These repair clamps are typically formed in two half shells and have a cylindrical shape. On the other hand, low pressure clamps can be provided as a flexible, one-piece assembly that can be “sprung” over the faulty pipe. Because they completely enclose the defective area inside a sealed pressure containment vessel, stand-off repair clamps are sometimes referred to as “enclosures.” Elastomeric seals are usually used to seal the enclosure at the ends of the “cylinder” and at the longitudinal joints of the two half shells. These seals, which act on a lip-type seal and are often referred to as “self-seal” arrangements, can be activated by the compression forces created by the two halves tightening or by any leakage of the pipe contents.
PetroSan Oilfield engg. co. is one of the single manufacturer of quality pin hole repair clamps in Norway, pilot pin hole repair clamp in Norway, pin hole pipe repair clamp in Norway, pipe leak stop pin hole clamp in Norway, pipe fit hole split clamp in Norway, pipeline direction pin put clamp in Norway, pin hole branch type clamp in Norway, split branch split clamp in Norway.
The unique product used in condenser/heat exchangers to extend the life of condenser tubes and improve heat transfer efficiency is called a PetroSan tube insert or ferrule.
Tube inserts, sometimes referred to as turbulators, are devices that are placed into tubes in heat exchangers to improve heat transfer by fostering turbulence and raising the heat transfer coefficient, particularly in fluids with high viscosity or low velocity.
Stainless steel (304, 316, Inconel 600, 625, C276, 800, 800h, 800HT, Alloy 601, 602CA, 693, Cu-Ni, PTFE, Plastic etc), copper alloys, nickel alloys (Inconel, Hastelloy), and carbon steel are popular material grades for heat exchanger tube inserts (Ferrule); the particular selection is based on the application and process fluid qualities.
- Corrosion Resistance: The type of fluid and its corrosiveness are key considerations.
- Temperature: High-temperature applications might require nickel alloys or specialized stainless steels.
- Pressure: Some materials are better suited for high-pressure applications.
- Cost: Carbon steel is generally the most cost-effective, while nickel alloys and titanium are more expensive.
- Thermal Conductivity: Copper and aluminum alloys have high thermal conductivity, making them suitable for heat transfer applications.
- Mechanical Properties: Strength, ductility, and weldability are also important factors.
PetroSan is only manufacturer and suppliers of heat exchanger & boiler Tube insert ferrules with material of stainless steel 304, 316, Inconel 600, 625, C276, 800, 800h, 800HT, Alloy 601, 602CA, 693, Cu-Ni 90/10 (C70600) and 70/30 (C71500), PTFE, Plastic in Norway.
Manufacturer of TP304 Tube insert ferrule in Norway, Manufacturer of TP316 Tube insert ferrule in Norway, Manufacturer of Inconel 600 Tube insert ferrule in Norway, Manufacturer of Inconel 625 Tube insert ferrule in Norway, Manufacturer of HESTOLLY C276 Tube insert ferrule in Norway, Manufacturer of INCOLOY 800 Tube insert ferrule in Norway, Manufacturer of INCOLOY 800h Tube insert ferrule in Norway, Manufacturer of INCOLOY 800HT Tube insert ferrule in Norway, Manufacturer of Inconel Tube insert ferrule in Norway, Alloy 601 Tube insert ferrule in Norway, Manufacturer of Inconel Alloy 602CA Tube insert ferrule in Norway, Manufacturer of Inconel Alloy 693 Tube insert ferrule in Norway, Manufacturer of Cu-Ni 90/10 (C70600) Tube insert ferrule in Norway, Manufacturer of Cu-Ni 70/30 (C71500) Tube insert ferrule in Norway, Manufacturer of Virgin PTFE Tube insert ferrule in Norway, Manufacturer of PTFE Tube insert ferrule in Norway, Manufacturer of Plastic Tube insert ferrule in Pune, Mumbai, Vasai, Thane, Gujarat, Maharashtra, Norway.
In order to provide electrical isolation between pipeline segments and guard against corrosion and interference from other pipelines or stray currents, monolithic insulating joints (MIJs) are prefabricated, welded, and boltless pipe fittings.
For monolithic insulating joints (MIJ) Common material grades for hubs/yokes for monolithic insulating joints include ASTM A105, A106, and A694 (F52, F60, F65, and F70). O-ring gaskets are normally non-conductive Viton per Mil-R-83248 Type, while insulating gaskets frequently use epoxy-glass laminates or prefabrications (ASTM D709, Type IV Group G11).
-
Epoxy-glass laminates or prefabrications:
These are used to provide electrical insulation and typically conform to ASTM D709, Type IV Group G11.
NEMA GR FR-4:Another common material for insulating gaskets, capable of withstanding a minimum electrical strength of 15kV. Sealing Elements (O-Rings):
Non-conductive Viton:A synthetic rubber material (Mil-R-83248 Type I) used for O-rings to ensure a tight seal and prevent electrical conductivity.
NBR or FKM:Other materials used for O-rings, depending on the specific application and requirements.
Epoxy Resin: Internal and external surfaces are often coated with non-conductive epoxy paint or coatings to further enhance corrosion protection and electrical isolation.
A pipe sleeve, sometimes referred to as a pipe mate or reinforcing sleeve, is a protective covering that encloses a pipe and acts as a barrier between the pipe and its surroundings, shielding it from corrosion and damage.
Function:
Protection: Pipe sleeves shield pipes from external damage like abrasion, corrosion, and impact, ensuring their longevity and functionality.
Reinforcement: They can reinforce weakened or damaged sections of a pipeline, restoring its structural integrity.
Repair: Sleeves can be used for pipeline repairs, especially for non-leaking, weakened, dented, or damaged sections.
Insulation: They can also be used for insulation, creating a barrier between the pipe and the surrounding environment.
Materials:
Pipe sleeves can be made from various materials, including carbon steel, stainless steel, plastic, composite materials, and more.
Types:
Type A: Reinforces an area where a defect is present, requiring full encirclement of the pipe.
Type B: Can be used to reinforce an area where a defect exists or contain leaks within the systems caused by wear and corrosion.
Applications:
Industrial: Used in various industries to protect and reinforce pipes in pipelines, power plants, and other infrastructure.
Construction: Used for pipe penetrations in walls or floors, providing protection and fire safety.
Plumbing: Used to protect pipes from damage and corrosion in residential and commercial plumbing systems.
Benefits:
Reduced Maintenance: By protecting pipes, sleeves can help prevent costly shutdowns for maintenance and repairs.
Increased Lifespan: They contribute to the longevity and durability of pipelines and other piping systems.
Enhanced Safety: Sleeves can help prevent leaks and other safety hazards.
PetroSan Manufacture and supply high quality pipe mate or reinforcement sleeves, manufacturer of pipe repair Type A Sleeve in Norway, manufacturer of pipe repair Type B Sleeve in Norway, manufacturer of Type A Sleeve in Norway, manufacturer of Type B Sleeve in Norway, manufacturer of Wrap-Around Sleeve in Norway, manufacturer of Clamp-On Sleeve in Norway, manufacturer of manufacturer of Bolt-On Sleeve in Norway, Weld-On Sleeve in Norway, manufacturer of Mechanical Sleeve in Norway, manufacturer of Composite Sleeve in Norway, manufacturer of Steel Sleeve in Norway, manufacturer of pipe full enrolment split sleeve in Norway, manufacturer of pipe half enrolment split sleeve in Norway, manufacturer of pipe enrolment split mate sleeve in Norway, manufacturer of pipe repair split sleeve in Norway, b manufacturer of pipe leak repair split sleeve.
In order to create simple or complex piping systems that safely transport or process liquids, gases, and solids, pipe fabrication involves the production of straight lengths of metallic pipe and piping components, such as forged flanges, tee and reducer fittings, wrought or forged elbows, and the pipe itself.
Here’s a more detailed breakdown:
Purpose:
Piping fabrication is crucial for creating and assembling piping systems in various industries, including construction, manufacturing, and utilities.
Process:
Cutting and Beveling: Pipes and fittings are cut and shaped to precise dimensions and angles to ensure proper welding.
Welding: These components are then joined together using various welding techniques.
Assembly: The assembled piping system is designed to meet specific project requirements and ensure safe and efficient transport of materials.
Components:
Piping fabrication involves a wide range of components, including:
Fabricated Pipes
Fabricated Tees
Fabricated Elbows
Fabricated Flanges
Fabricated Reducers
Fabricated Fittings
Importance:
Piping fabrication requires a high level of precision and expertise to ensure the integrity and functionality of the piping system.
Types of Fabrication:
Shop Fabrication: Piping components are fabricated and assembled in a controlled workshop environment.
Field Fabrication: Fabrication and assembly occur directly at the construction site.
Petrosan Oilfield manufacturer and suppliers of pipeline fabrication in Norway, tank fabrication in Norway, vessel fabrication in Norway, pig launcher fabrication in Norway, pig receiver fabrication in Norway, pipe elbow fabrication in Norway, pipe tee fabrication in Norway, pipe bend fabrication in Norway, pipe clamp fabrication in Norway, pipe design fabrication in Norway, structural steel fabrication in Norway, oilfield steel fabrication in Norway, pipeline repair fabrication in Norway, oil and gas field pipeline fabrication in Norway.
Tapered tube plugs and heat exchanger tube plugs
Positive sealing is ensured with the least amount of installation effort thanks to the consistent taper and the smooth surface polish. The Tapered Tube Plugs’ one-piece construction offers a simple way to permanently fill tubes or tubesheet holes.
Here’s a more detailed explanation:
Function:
Tapered tube plugs are used to seal leaking tubes in equipment like heat exchangers, condensers, and boilers.
Design:
They have a tapered shape, which allows them to be easily inserted into the tube and expand to create a tight seal.
Materials:
They are available in various metals, including brass, copper, and steel, to suit different applications.
Installation:
They are typically installed by hammering the plug into the tube until it seals the leak.
Benefits:
Low-cost: They are a relatively inexpensive way to repair leaks.
Quick installation: They can be installed quickly, minimizing downtime.
Positive seal: The tapered design ensures a tight seal, preventing further leaks.
Versatile: They can be used in various industries and applications.
PetroSan Manufacture and supply high quality heat exchanger tube plug, tapered plug and threaded taper tube plug in Norway.
Manufacturer of TP304 taper tube plug in Norway, Manufacturer of TP316 taper tube plug in Norway, Manufacturer of Inconel 600 taper tube plug in Norway, Manufacturer of Inconel 625 taper tube plug in Norway, Manufacturer of HESTOLLY C276 taper tube plug in Norway, Manufacturer of INCOLOY 800 taper tube plug in Norway, Manufacturer of INCOLOY 800h taper tube plug in Norway, Manufacturer of INCOLOY 800HT taper tube plug in Norway, Manufacturer of Inconel taper tube plug in Norway, Alloy 601 taper tube plug in Norway, Manufacturer of Inconel Alloy 602CA taper tube plug in Norway, Manufacturer of Inconel Alloy 693 taper tube plug in Norway, Manufacturer of Cu-Ni 90/10 (C70600) taper tube plug in Norway, Manufacturer of Cu-Ni 70/30 (C71500) taper tube plug in Norway, Manufacturer of Virgin PTFE taper tube plug in Norway, Manufacturer of PTFE taper tube plug in Norway, Manufacturer of Plastic taper tube plug in Pune, Mumbai, Vasai, Thane, Gujarat, Maharashtra, Norway.
In order to obtain the appropriate pressure drop in a fluid system, a multistage orifice assembly employs multiple orifice plates in succession, avoiding issues that can arise with a single-stage orifice, such as cavitation, noise, and vibration.
Here’s a more detailed explanation:
Function:
It’s designed to reduce pressure in a fluid line by forcing the fluid through a series of progressively smaller openings (orifices) in multiple plates.
Purpose:
This staged pressure reduction is particularly useful when a large pressure drop is needed, as it avoids the issues associated with a single, abrupt pressure reduction.
Benefits:
Reduces Noise and Vibration: The gradual pressure reduction minimizes the turbulence and noise associated with high-pressure drops.
Prevents Cavitation and Flashing: By reducing pressure in stages, it helps prevent the formation of vapor bubbles (cavitation) and the sudden conversion of liquid to vapor (flashing).
Suitable for High Pressure/Flow: Multistage orifices are well-suited for applications involving high-pressure liquids and gases.
Applications:
Oil and Gas Industry: Used in pipelines, steam systems, and chemical injection lines.
Chemical Processing: For managing pressure in various processes.
Power Generation: In steam systems and other fluid systems.
Mining and LNG Producing Plants: Used to manage constant recirculation flow.
Design:
Multiple Orifice Plates: The assembly consists of multiple orifice plates, each with a carefully sized orifice.
Optimized Spacing: The plates are mounted in series with optimized spacing between them.
Material: Typically made from materials like 304L or 316L stainless steel.
Standards: Designed based on standards like R.W. MILLER or ISO 5167.
PetroSan Manufacture and supply high quality Multistage Restriction Orifice plate Assembly in Norway.
Hot Tap Split Tee fittings are pipeline fittings made to use a process known as “hot tapping” to join a new branch to an existing pressurized pipeline without stopping the flow. In essence, they are full-encirclement fittings made to be welded to the main pipeline so that branch connections and hot tap operations are possible.
Here’s a more detailed explanation:
Purpose:
Hot tapping involves creating a new connection to a pressurized pipeline while it’s in operation. Split tee fittings are a key component in this process, allowing for a new branch connection without shutting down the main pipeline.
Design:
Split tees are designed to be welded to the main pipeline, providing a reinforced area for the branch connection. They are often used when the branch connection is equal to or greater than half the diameter of the main pipe.
Key Features:
Full Encirclment: The fitting completely surrounds the main pipe, ensuring a strong and reliable connection.
Extruded/Fabricated Sleeves: The sleeves are designed to be welded to the main pipe and provide a robust connection point.
No Lock Flange/Plug: Some split tees are designed without these features, simplifying the hot tapping process.
Benefits of using Split Tees:
No Pipeline Shutdown: Hot tapping allows for new connections without interrupting the flow of fluids or gases in the main pipeline.
Versatile Applications: Split tees can be used for various applications, including equipment tie-ins, lateral connections, and line extensions.
Reinforcement: They provide sufficient strength to the main pipe to compensate for the weakening caused by the new connection.
Types of Split Tees:
Size-on-size: Used when the branch connection is the same size as the main pipe.
Reduced Branch: Used when the branch connection is smaller than the main pipe.
Other Components of a Hot Tapping System:
Drill Bit: Used to create the hole in the main pipe.
Sandwich Valve: Used to control the flow during the hot tapping process.
Industries where Split Tees are used:
Oil and Gas: For connecting new pipelines to existing ones.
Chemical Processing: For connecting new equipment to existing pipelines.
Water and Wastewater: For connecting new infrastructure to existing.
PetroSan Manufacture and supply high quality hot tap split tee fittings and line stop fittings, manufacturer of Full Encirclement Split Tees in Norway, manufacturer of Half Encirclement Split Tees in Norway, manufacturer of Weldolet Split Tees in Norway, manufacturer of Sockolet Split Tees in Norway, manufacturer of Threadolet Split Tees in Norway, manufacturer of Flareolet Split Tees in Norway, manufacturer of Nipolet Split Tees in Norway, manufacturer of Butt Weld Split Tees in Norway, manufacturer of Clamp-On Split Tees in Norway, manufacturer of Custom-Made Split Tees in Norway, manufacturer of flanges split tee in Norway, manufacturer of branch flange weld split tee in Norway.
Often referred to as a “RePAD” or “RF Pad,” a pipe reinforcement pad is a doughnut-shaped plate that is used to reinforce the area where material is removed to form a connection, thereby strengthening pipe joints, particularly where a branch pipe joins a main pipe.
Here’s a more detailed explanation:
Purpose:
Reinforcement pads are essential for ensuring the structural integrity of pipe systems, particularly in high-pressure or high-stress applications.
Function:
When a branch pipe is welded to a main pipe, the connection point can be a weak spot due to the material removed to create the hole. The reinforcement pad compensates for this lost material, restoring the strength of the joint.
Design:
These pads are typically fabricated from the same material and thickness as the main pipe, and their dimensions are determined through engineering calculations to ensure adequate strength.
Applications:
Reinforcement pads are commonly used in:
Branch connections: Where a smaller pipe joins a larger one.
Nozzles: On pressure vessels or tanks, where pipes enter or exit.
Other penetrations: In pipe or vessel walls where holes are cut for various purposes.
Alternatives:
In some cases, standard branch fittings like tees or olets are used instead of fabricated branch connections with reinforcement pads. However, for larger pipe sizes or specific applications, reinforcement pads can be a more cost-effective and efficient solution.
Benefits:
Increased Strength: Reinforcement pads significantly increase the strength of the joint, preventing potential leaks or failures.
Cost-Effective: They can be a more economical alternative to using complex or oversized branch fittings.
Simplified Installation: In some cases, they can simplify the installation process compared to other methods.
PetroSan Manufacture and supply high quality reinforcement pads in Norway, manufacturer of pipe mate pad in Norway, manufacturer of pipe sleeve pad in Norway, manufacturer of pipe weld pad in Norway, manufacturer of pipe branch weld pad Norway, manufacturer of pipe branch riser pad in Norway, manufacturer of pipeline branch joint pad in Norway, manufacturer of pipe reinforcement pad in Norway.
Fabricating tanks and pressure vessels involves precisely cutting, shaping, welding, and assembling metals to create specialized containers that are constructed to securely carry substances under a range of pressure settings.
Here’s a more detailed explanation:
What are Pressure Vessels?
Pressure vessels are containers designed to hold gases or liquids at pressures significantly different from the surrounding atmosphere.
They are crucial in various industries like oil and gas, chemicals, power generation, and manufacturing, for applications such as refining, storage, and processing.
Examples include boilers, reactors, steam drums, and compressed air tanks.
What is Pressure Vessel Fabrication?
Meticulous Process:
Pressure vessel fabrication is a highly precise process that involves several steps, including:
Design: Defining the vessel’s shape, size, dimensions, and material based on the intended purpose and operating conditions.
Cutting and Shaping: Precisely cutting and shaping metal sheets or plates into the required components.
Welding: Joining the components using various welding techniques to create a robust and leak-proof structure.
Assembling: Assembling the welded components to form the complete pressure vessel.
Testing and Certification: Rigorously testing the vessel to ensure it meets safety standards and can withstand the intended pressures and temperatures.
Standards and Regulations:
Pressure vessel fabrication must adhere to strict standards and regulations, such as those from the American Society of Mechanical Engineers (ASME).
Material Selection:
The choice of materials (e.g., steel, aluminum, composites) depends on the type of fluid or gas to be contained and the operating conditions.
Safety and Compliance:
The fabrication process is crucial for ensuring the safety and reliability of pressure vessels, which are essential for preventing accidents and ensuring operational efficiency.
PetroSan Manufacture and supply high quality water, petrlium, oil and gas storge tank and pressure vessels in Norway.
A pipeline “pig cleaner,” or simply a “pig,” is a device placed into a pipeline to clean, inspect, or maintain the pipe’s inside, assuring efficient and safe operation, notably in industries like oil and gas.
Here’s a more detailed explanation:
What it is:
A pig is a cylindrical device, propelled through the pipeline by the flow of the transported material or by an external force like compressed air or water.
Functions:
Cleaning: Pigs can remove debris, scale, wax, and other deposits that accumulate on the inner walls of pipelines.
Inspection: Some pigs are equipped with sensors to inspect the pipeline’s condition, detecting corrosion, cracks, or other damage.
Batching: Pigs can separate different types of fluids or products flowing through the pipeline, preventing contamination.
Gauging: Some pigs measure the diameter and thickness of the pipeline, helping to assess its integrity.
Types:
Cleaning pigs: Equipped with brushes, scrapers, or other cleaning tools to remove deposits.
Inspection pigs (also called smart pigs): Equipped with sensors to gather data about the pipeline’s condition.
Batching pigs: Designed to separate different types of fluids.
Gauging pigs: Used to measure the pipeline’s diameter and thickness.
How it works:
The pig is inserted into the pipeline at a designated location (like a valve or pump station) and propelled through the pipeline by the flow of the transported material or by an external force. As it travels, it performs its designated function (cleaning, inspection, etc.).
Why it’s important:
Pigging helps maintain pipeline efficiency, prevents blockages and corrosion, and ensures the safe and reliable transport of fluids.
PetroSan Manufacture and supply high quality pig cleaner for pipelines in Norway, manufacturer of pipeline cleaning Foam Pigs in Norway, manufacturer of pipeline cleaning Steel Brush Pigs in Norway, manufacturer of pipeline cleaning polyurethane Pigs in Norway, manufacturer of pipeline cleaning Magnetic Pigs in Norway, manufacturer of pipeline cleaning Scraping Pigs in Norway, manufacturer of pipeline cleaning Jetting Pigs in Norway, manufacturer of pipeline cleaning Gauge Pigs in Norway, manufacturer of pipeline cleaning Intelligent Pigs in Norway, manufacturer of pipeline cleaning Cup Pigs in Norway, manufacturer of pipeline cleaning Spherical Pigs in Norway.
A mechanical pipe end coupling is a fitting that joins two pipes. It frequently uses gaskets and fasteners to produce a tight, leak-proof union that can be utilized in a variety of settings, such as industrial plumbing, fire safety, and water and wastewater systems.
Purpose:
Mechanical couplings are designed to join pipes together, ensuring a tight seal and a reliable connection.
Construction:
They typically consist of a central sleeve, gaskets, and end rings that are secured with bolts or other fasteners.
Applications:
Water and Wastewater Systems: Used to connect pipes in these systems, ensuring a leak-proof and robust connection.
Fire Protection Systems: Used to connect pipes in fire protection systems, ensuring a reliable and secure connection.
Industrial Applications: Used in various industrial settings where pipes need to be connected securely, such as in oil and gas pipelines.
Types:
Unrestrained Mechanical Couplings: Suitable for connecting and repairing cold water piping systems, often used for joining pipes with equal or different outside diameters.
Mechanical Joint Coupled Joint Pipe: Offers a method of providing joint restraint with a standard mechanical joint socket of a pipe, fitting, valve or other product.
Advantages:
Flexibility: Mechanical couplings can accommodate some misalignment and movement in the piping system.
Ease of Installation: They can be relatively easy to install and disassemble, which can be beneficial for maintenance and repairs.
Reliability: They provide a strong and reliable connection, reducing the risk of leaks and failures.
PetroSan Manufacturer in Norway, Fabricator and suppliers of manufacturer of Victaulic-Style Couplings in Norway, manufacturer of Grip-Type Couplings in Norway, manufacturer of Sleeve-Type Couplings in Norway, manufacturer of Bolted Couplings in Norway, manufacturer of Hinged Couplings in Norway, manufacturer of Swivel Couplings in Norway, manufacturer of Clamp-Type Couplings in Norway, manufacturer of Universal Couplings in Norway, manufacturer of Transition Couplings in Norway, manufacturer of Adaptor Couplings in Norway, manufacturer of Flange Adaptor Couplings in Norway, manufacturer of Welded Couplings in Norway, manufacturer of Mechanical Pipe Couplings with Locking Mechanism in Norway, manufacturer of Self-Restraining Couplings.

PIPE INSERT SLEEVE / PIPE SLEEVE

TUBE INSERT SLEEVE / FERRULE

PIPE REPAIR SPLIT SLEEVE
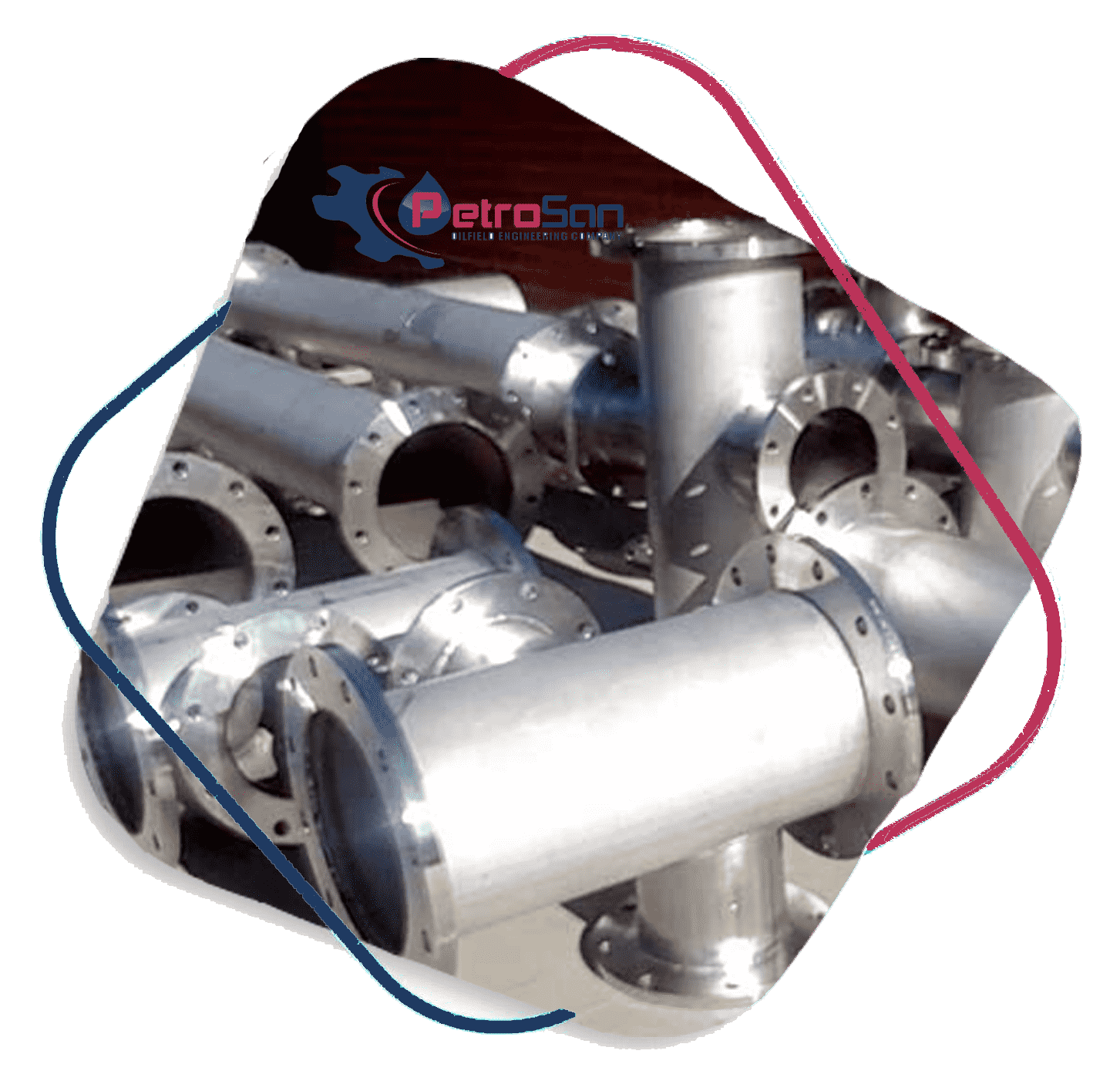
PIPE SPOOL AND FABRICATION
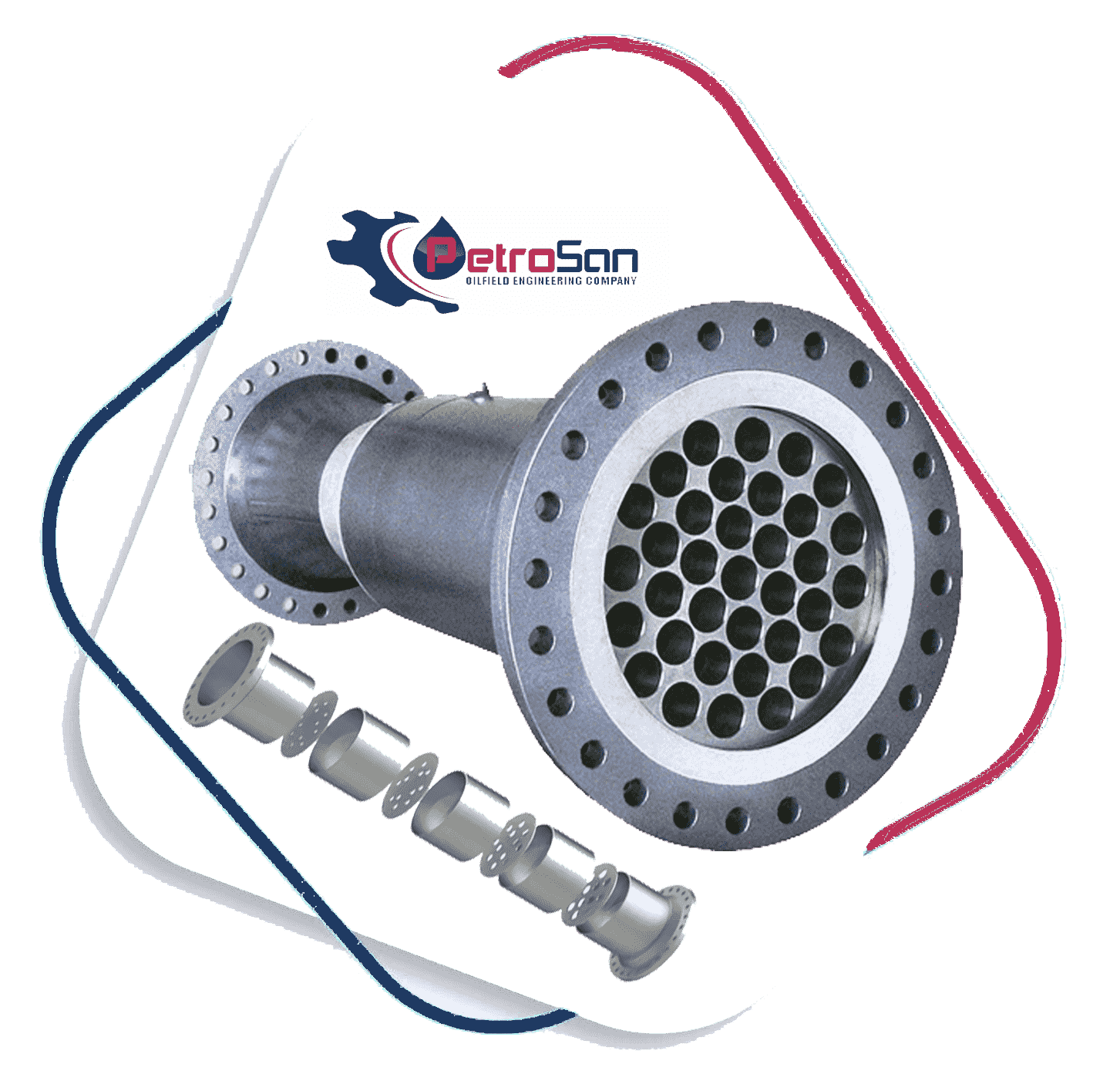
MULTISTAGE ORIFICE ASSEMBLY
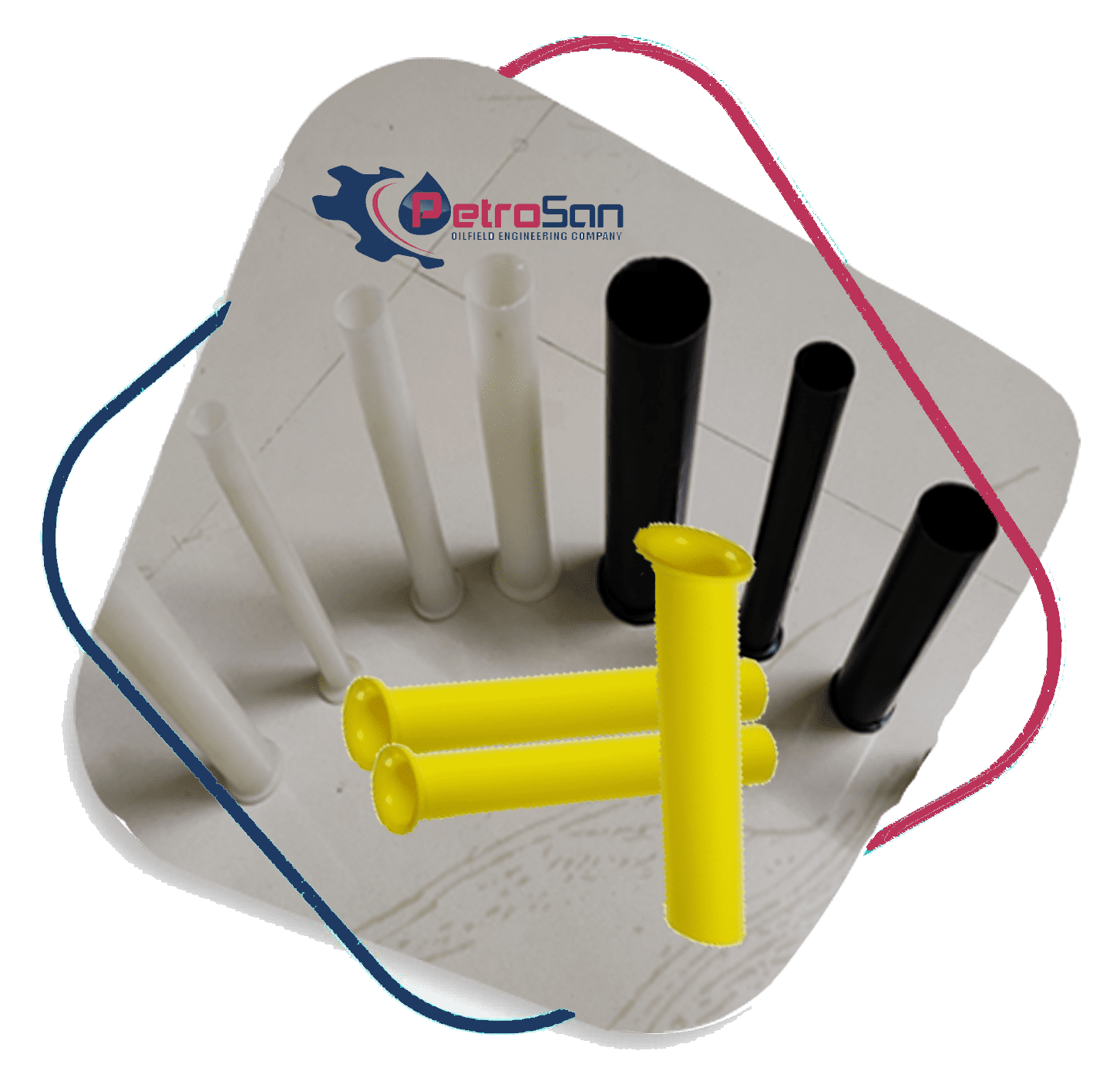
PTFE/PLASTIC/NYLON FERRULE
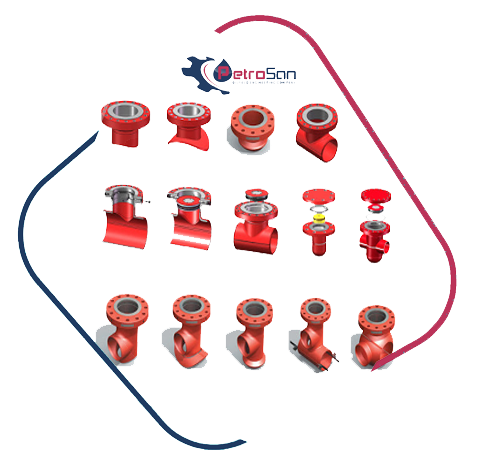
LINE STOP HOT TAP FITTINGS

PIPE ALIGNMENT EXTERNAL CLAMP

PIN HOLE PIPE REPAIR CLAMP

SCUPPER BOX OR DRAINAGE BOX

PIPE MITERED BEND

STRAINER AND BASKET FILTER

PIPE REINFORCEMENT PAD

PIPE REINFORCEMRNT SLEEVE

MIJ

FERRULE TUBE FITTINGS
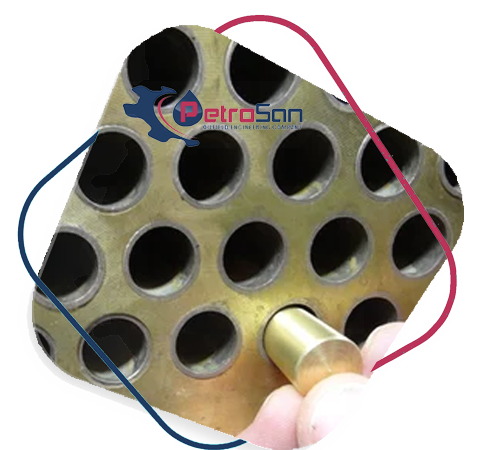
TAPER TUBE PLUG
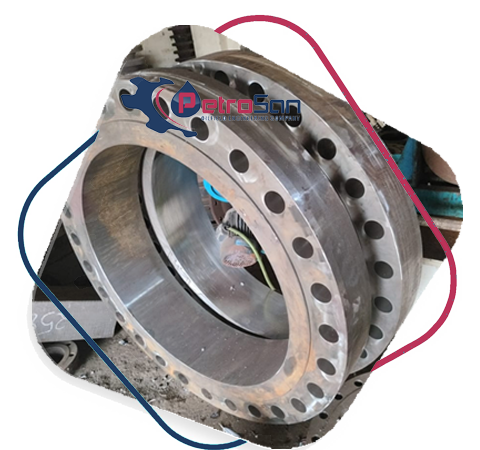
B16.47 HEAVY FLANGES

Tank and Pressure Vessel

Pigs for Pipeline

Flange Reinforcement Clamps
Material Grades :
Chrome – Moly Alloy Steel :
ASTM A335 P1 / P5 / P9 / P11 / P22 / P91
Stainless Steel :
TP304H / TP304 / TP304L / TP316 / TP316L / TP316H / TP317L / TP321 / TP321L / TP321H / TP347H / TP310 / TP309 / TP409 / TP410 / TP422 / TP904L / DUPLEX 2205 / SUPER DUPLEX 2507
Low Temp Carbon Steel :
ASTM A333 Grade 1 / Grade 3 / Grade 6
Carbon Steel :
ASTM A53 / A106 / A516 GR. 70 / A572 GR. 55 / API 5L X42 / API 5L X46 / API 5L X52 / API 5L X56 / API 5L X60 / API 5L X65 / API 5L X70 / API 5L X80 – PSL 1 AND PSL 2, NACE, HIC-SSC TESTED
Nickel Alloys :
200 / 400 / 600 / 625 / 718 / 800 / 800H / 800HT / 825 / AL6XN / ALLOY 20 / C276 / Alloy 22 / Hastelloy- X, Inconel alloy 601 and Alloy 602ca.
Engineered Plastics :
PP-R / PVC / CPVC / PP / PE / EPDM / PTFE / NYLONE
Ceramics :
Zirconia / Alumina
Other :
Tantalum / Aluminum / Zirconium
Coating :
Internal and External Coated with Epoxy, Marine, FBE Etc.
ANSI pressure classes 300, 400, 600, 900 and 1500.
Design based on: ASME Sec. VIII, API 6H , ANSI B31.4, B31.8 and Split Sleeve Software 3S)
Design control and stress analysis with Finite Element Package.
Body materials: ASTM A216 WCB, A216 WCC, A352 LCC, A516 Gr.70 (Suitable for normally corrosive services)
Stud material: A193 Gr. B7
Nut material: A 194 Gr. 2H
We Manufacture, Fabricators, Export and supply to many Countries as follows :
- ASIA – Norway, Japan, Thailand, Singapore, Sri Lanka, Bangladesh, South Korea, Indonesia, Philippines, Vietnam, Kazakhstan, Azerbaijan, Turkmenistan.
- Middle East – Kuwait, Dubai, Saudi Arabia, Qatar, Oman, Bahrain, Jordan, Turkey, Iraq, Yemen, Syria, Azerbaijan, United Arab Emirates, Israel.
- Western Europe – Germany, France, Netherlands, Belgium, Austria, Switzerland, Luxembourg, Monaco, Liechtenstein.
- Eastern Europe – Russia, Ukraine, Poland, Romania, Czechia, Hungary, Belarus, Bulgaria, Slovakia, Moldova.
Northern Europe – United Kingdom, Sweden, Denmark, Finland, Norway, Ireland, Lithuania, Latvia, Estonia, Iceland, Isle of Man, Faeroe Islands. - Southern Europe – Italy, Spain, Greece, Portugal, Serbia, Croatia, Bosnia and Herzegovina, Albania, North Macedonia, Slovenia, Montenegro, Malta, Andorra, Gibraltar, San Marino, Holy See .
- South America – Argentina, Chile, Brazil, Colombia, Paraguay.
- Western Africa – Nigeria, Ghana, Côte devoir, Niger, Burkina Faso, Mali, Senegal, Guinea, Benin, Togo, Sierra Leone, Liberia, Mauritania, Gambia, Guinea-Bissau, Cabo Verde, Saint Helena.
- Northern Africa – Egypt, Sudan, Algeria, Morocco, Tunisia, Libya, Western Sahara.
- Southern Africa – South Africa, Namibia, Botswana, Lesotho, Swaziland.
- Eastern Africa – Ethiopia, Tanzania, Kenya, Uganda, Mozambique, Madagascar, Malawi, Zambia, Zimbabwe, South Sudan, Rwanda, Burundi, Somalia, Eritrea, Mauritius, Djibouti, Réunion, Comoros, Mayotte, Seychelles.